O processo de injeção é a forma mais versátil de produzir peças e produtos plásticos. É rápido, funciona com uma variedade de termoplásticos e pode resultar em um protótipo ou produto final durável e altamente detalhado!
Mas o processo é complexo e cheio de desafios. Felizmente, muitos deles são fáceis de resolver! Abaixo você confere os 5 principais problemas e soluções no processo de injeção plástica.
A Madeiplast é especializada em todos os processos de confecção de moldes e moldagem de peças plásticas por injeção. Solicite seu orçamento, em breve retornamos seu contato para conversarmos sobre a demanda da sua indústria.
Você também vai gostar de saber:
➡️ Tudo sobre injeção plástica automotiva
➡️ A importância do projeto do molde?
➡️ Saiba tudo sobre o ciclo de injeção!
Problemas e soluções no processo de injeção
De modo geral, os problemas no processo de injeção plástica podem ocorrer:
➡️ No projeto de molde
➡️ Na máquina injetora
➡️ Com a matéria-prima e sua preparação
➡️ No ambiente de trabalho e operador do maquinário
Nesse sentido, os 5 principais problemas na moldagem por injeção são:
🔶 Rebarbas
🔶 Descoloração
🔶 Injeção incompleta
🔶 Fragilidade da peça
🔶 Deformações
Abaixo você confere por que acontecem e como solucionar cada um deles.
1 – Rebarbas
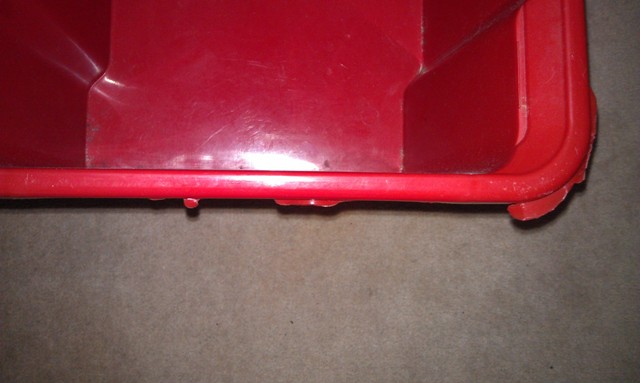
Excesso de material moldado que aparece como saliência na borda da peça ejetada. A rebarba aparece porque o material fluiu para fora dos canais de fluxo pretendidos e para o espaço entre as placas de ferramentas ou no pino do injetor.
Esse tipo de defeito geralmente é sutil, mas pode ser considerado um grande problema se for particularmente óbvio em um produto. O processo para retrabalhar um produto moldado com rebarbas geralmente inclui aparar o excesso de material.
Causas:
❌Um molde mal projetado ou desgastado e degradado é o contribuinte mais comum para o surgimento de rebarbas.
❌Temperatura do molde ou pressão de injeção excessivamente altas também podem causar esse defeito.
❌O material que flui através das cavidades do molde pode forçar seu caminho entre as placas quando a força de fixação da placa é inadequada.
Soluções:
✔️Reequipe ou redesenhe o molde se as placas não se encaixarem corretamente ou permitirem que o material flua para fora do canal.
✔️Aumente a força de fixação da placa para limitar o fluxo de material ao canal.
✔️Ajuste a temperatura do molde, pressão de injeção e ventilação para melhorar o fluxo de material.
2 – Descoloração
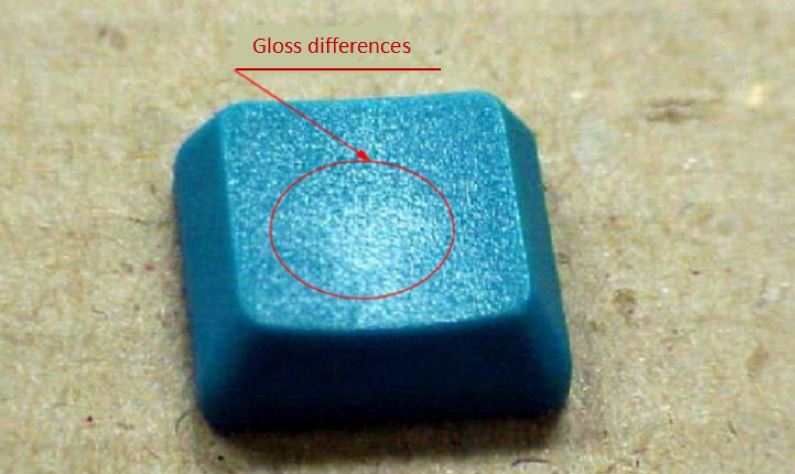
A descoloração, ou “estrias de cor”, ocorre quando uma peça moldada tem uma cor diferente da pretendida. Muitas vezes, a descoloração é limitada a uma área localizada ou a algumas listras de cor anormal na peça moldada.
Esse defeito normalmente afeta a aparência da peça sem reduzir sua resistência.
Causas:
❌Uma causa comum de descoloração são os pellets restantes na tremonha, ou resina residual no bico ou molde de uma produção anterior.
❌Pouca estabilidade térmica do agente de coloração ou mistura inadequada do masterbatch são outras causas potenciais.
Soluções:
✔️Certifique-se de que os trabalhadores limpem adequadamente a tremonha, o bocal e o molde entre as produções para eliminar quaisquer pellets residuais ou material de base.
✔️Considere usar um composto de purga para remover o excesso de cor da máquina.
✔️Certifique-se de estar usando um agente de cor com estabilidade térmica adequada.
✔️Certifique-se de que o masterbatch seja misturado uniformemente para uma saída de cores consistente.
3 – Injeção incompleta (mal preenchido)
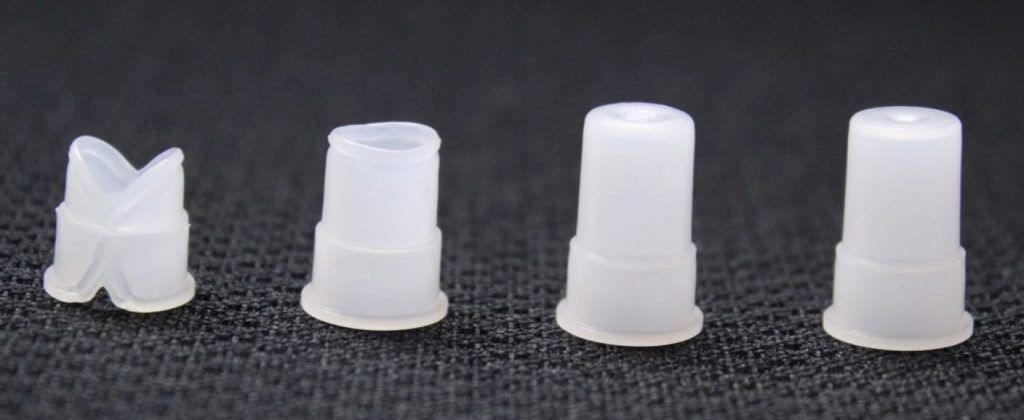
O fluxo de material fundido não preenche completamente as cavidades do molde. O resultado é que a peça plástica moldada fica incompleta após o resfriamento.
Este é um grande defeito, pois, pode inibir a função ou a aparência da peça moldada!
Causas:
❌A causa mais comum é a restrição de fluxo resultante de portas estreitas ou bloqueadas.
❌Às vezes, o material é muito viscoso ou o molde está muito frio para permitir que o material fundido preencha completamente o molde antes do resfriamento.
❌Outras vezes, bolsas de ar presas podem estar impedindo o fluxo adequado ou a pressão de injeção pode ser inadequada.
Soluções:
✔️Redesenhe o molde com canais ou portões mais largos para melhor fluxo.
✔️Aumente a velocidade ou pressão de injeção, ou escolha um material de base mais fino para melhorar o fluxo.
✔️Aumente a temperatura do molde para evitar que o material esfrie muito rapidamente.
✔️Adicione saídas de ar extras ou amplie as saídas existentes no molde para permitir que o ar preso escape.
4 – Fragilidade da peça
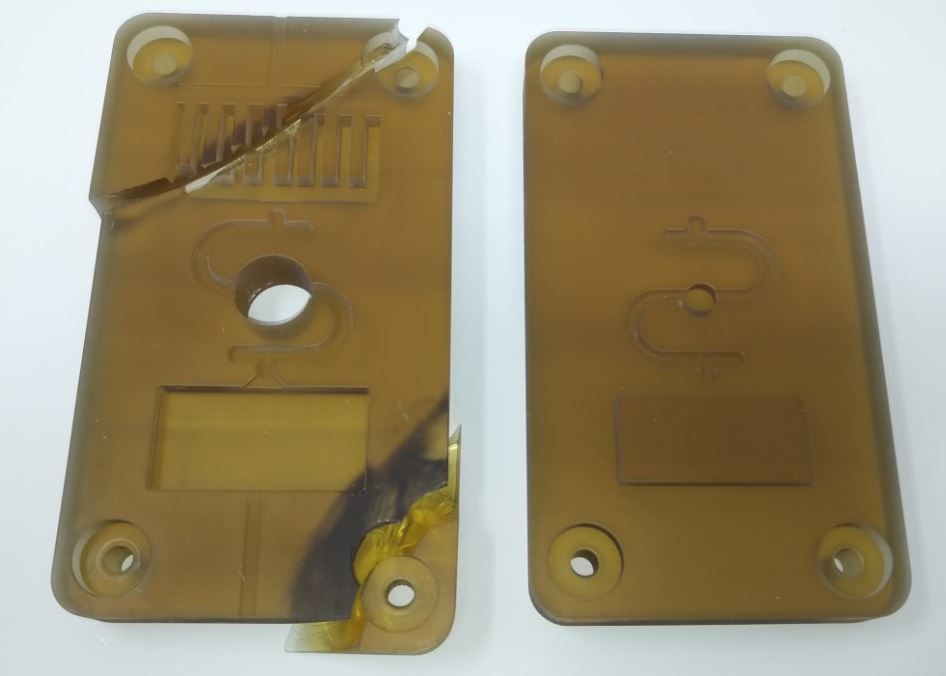
A fragilidade colabora para que a peça plástica seja facilmente rachada ou quebrada em algum lugar.
Causas:
❌A configuração da temperatura de injeção está incorreta.
❌As configurações do sistema de portão e canal não são apropriadas.
❌A força da marca de fusão não é alta.
Soluções:
✔️Projeto do molde: aumente o tamanho do corredor principal, corredor de ramificação e portão.
✔️Máquina: escolha um parafuso bem projetado para tornar a distribuição de temperatura mais uniforme durante a plastificação.
✔️Material: estabeleça condições de secagem adequadas antes da moldagem por injeção. Reduza o uso de materiais reciclados e aumente a proporção de matérias-primas. Use plástico de alta resistência!
✔️Processo: reduza a temperatura do cilindro e do bocal do material. Reduza a contrapressão, a velocidade do parafuso e a velocidade de injeção. Aumente a temperatura do material e a pressão de injeção, melhore a força de fusão.
5 – Deformações (empenamentos)
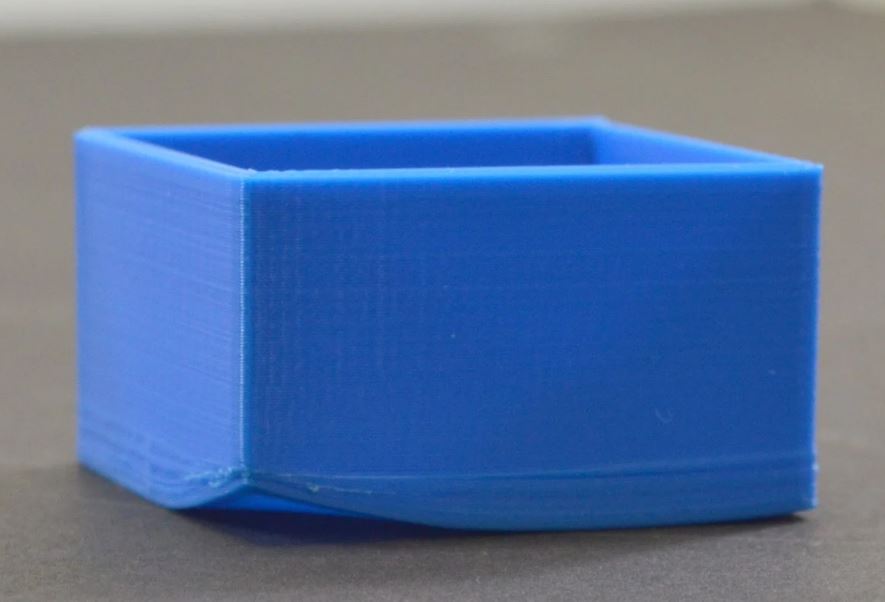
É a deformação que pode ocorrer em produtos moldados por injeção plástica quando diferentes partes de um componente encolhem de forma desigual.
Assim como a madeira pode deformar quando seca de forma desigual, o plástico e outros materiais podem deformar durante o processo de resfriamento. Isso é porque o encolhimento desigual coloca pressão indevida em diferentes áreas da peça moldada.
Esse estresse indevido resulta em flexão ou torção da peça acabada à medida que esfria. Isso é evidente em uma peça que deve ficar plana, mas deixa uma lacuna quando colocada em uma superfície plana.
Causas:
❌O resfriamento ocorreu muito rapidamente.
❌Muitas vezes, a temperatura excessiva ou a baixa condutividade térmica do material fundido podem piorar o problema.
❌Outras vezes, o projeto do molde pode contribuir para a deformação quando as paredes da ferramenta não são de espessura uniforme – o encolhimento aumenta com a espessura da parede.
Soluções:
✔️Certifique-se de que o processo de resfriamento seja gradual e longo o suficiente para evitar tensões desiguais no material.
✔️Abaixe a temperatura do material ou molde.
✔️Tente mudar para um material que encolhe menos durante o resfriamento (por exemplo, termoplásticos cheios de partículas encolhem muito menos do que materiais semicristalinos ou grades não preenchidas).
✔️Redesenhe o molde com espessura de parede uniforme e simetria da peça para garantir maior estabilidade na peça durante o resfriamento.
Processo de injeção de plástico sem preocupações é na Madeiplast
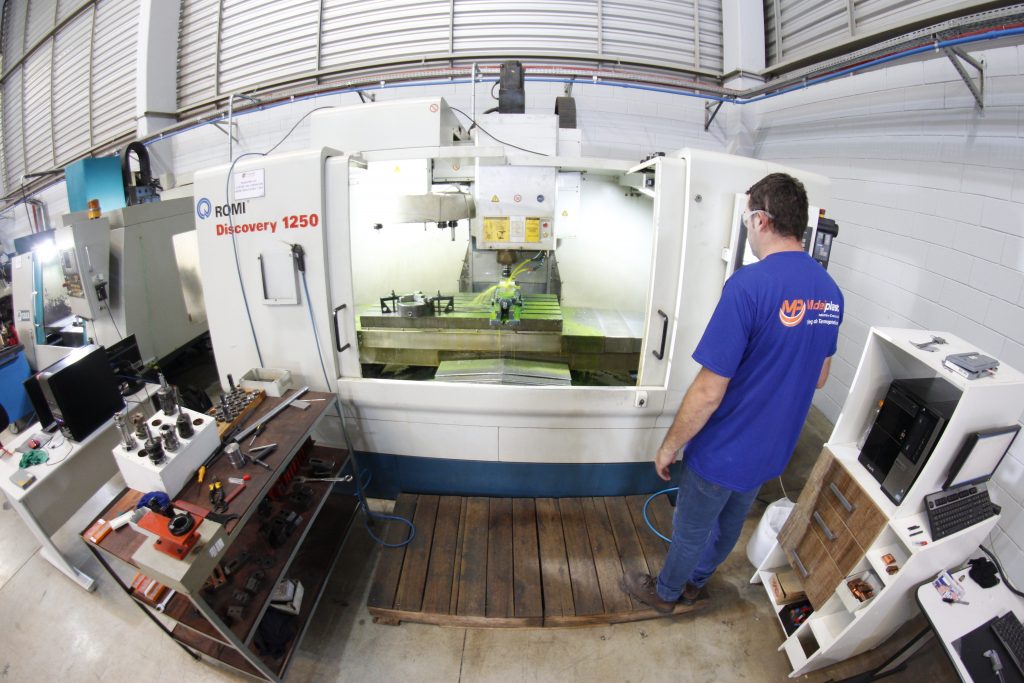
Nossa equipe experiente é capacitada para resolver até os problemas mais complexos com plásticos! Não importa qual seja o projeto ou o problema, trabalharemos com você para criar a solução ideal e fornecer peças moldadas por injeção de plástico personalizadas da mais alta qualidade!
Solicite um orçamento ou entre em contato conosco para iniciar seu próximo projeto. Respondemos rapidamente sua mensagem.